Plastic extrusion for extra-durable, long-lasting materials
Plastic extrusion for extra-durable, long-lasting materials
Blog Article
A Comprehensive Guide to the Refine and Benefits of Plastic Extrusion
In the large world of manufacturing, plastic extrusion arises as a vital and extremely effective process. Transmuting raw plastic into continuous accounts, it provides to a plethora of industries with its remarkable flexibility.
Recognizing the Basics of Plastic Extrusion
While it may show up complex at first glance, the process of plastic extrusion is essentially basic. The process begins with the feeding of plastic product, in the kind of granules, pellets, or powders, right into a warmed barrel. The shaped plastic is after that cooled down, strengthened, and cut right into wanted lengths, completing the procedure.
The Technical Process of Plastic Extrusion Explained
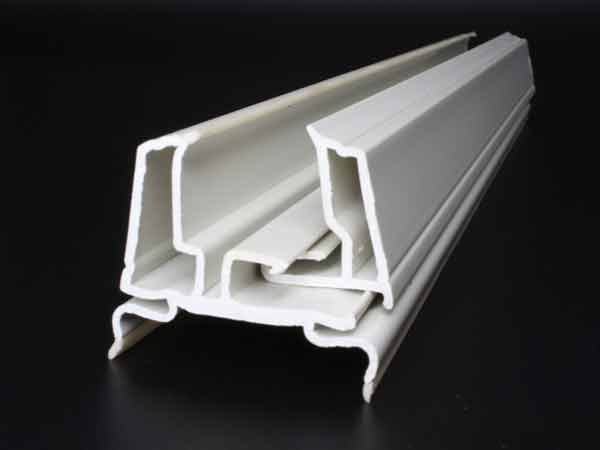
Sorts Of Plastic Suitable for Extrusion
The choice of the right kind of plastic is a critical facet of the extrusion process. Different plastics provide unique homes, making them extra matched to certain applications. Polyethylene, for instance, is frequently used due to its reduced cost and simple formability. It supplies outstanding resistance to chemicals and wetness, making it excellent for items like tubes and containers. Similarly, polypropylene is another popular choice due to its high melting point and resistance to fatigue. For even more robust applications, polystyrene and PVC (polyvinyl chloride) are usually picked for their stamina and toughness. Although these prevail choices, the choice eventually depends upon the details demands of the item being created. So, recognizing these plastic types can considerably boost the extrusion procedure.
Comparing Plastic Extrusion to Various Other Plastic Forming Methods
Comprehending the types of plastic ideal for extrusion paves the means for a more comprehensive conversation on how plastic extrusion piles up versus various other plastic forming methods. Plastic extrusion is unparalleled when it comes to creating constant accounts, such as gaskets, pipes, and seals. It additionally enables for a constant cross-section along the size of the product.
Key Benefits of Plastic Extrusion in Production
In the world of manufacturing, plastic extrusion uses numerous substantial benefits. One significant benefit is the cost-effectiveness of the procedure, which makes it an economically appealing production technique. Additionally, this method gives remarkable product adaptability and boosted production speed, thus boosting general production performance.
Economical Production Method
Plastic extrusion jumps to the forefront as an economical manufacturing approach in manufacturing. This procedure stands apart for its ability to create high volumes of product promptly and effectively, supplying producers with substantial cost savings. The key cost benefit is the ability to use less costly raw products. Extrusion makes use of thermoplastic materials, which are less expensive compared to ceramics or steels. Even more, the extrusion process itself is relatively straightforward, decreasing labor prices. Additionally, plastic extrusion needs much less energy than conventional manufacturing approaches, contributing to reduced functional costs. The process likewise decreases waste, as any faulty or excess products can be reused and reused, supplying another layer of cost-effectiveness. In general, the monetary advantages make plastic extrusion a highly attractive option in the production market.
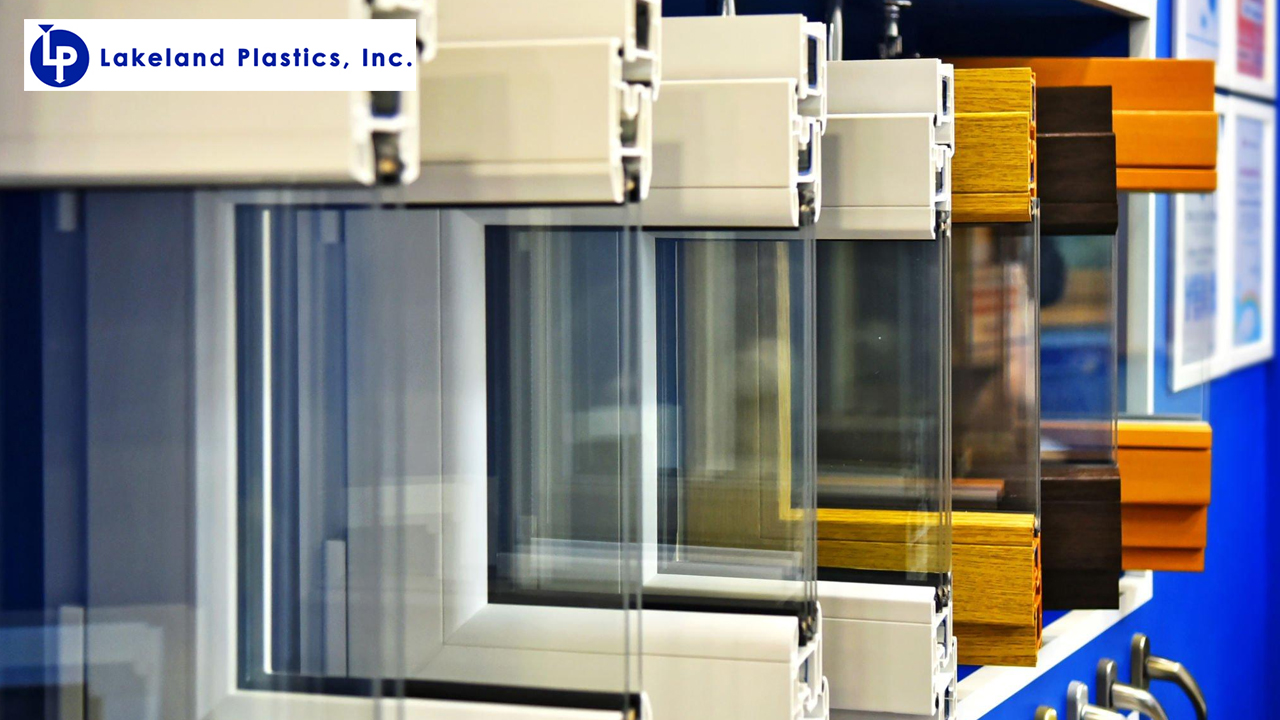
Superior Item Adaptability
Beyond the cost-effectiveness of plastic extrusion, another considerable advantage in manufacturing depend on its remarkable product flexibility. This procedure permits for the production of a large range of products with varying forms, dimensions, and designs, from straightforward plastic sheets to intricate accounts. The moved here versatility is attributed to the extrusion die, which can be customized to yield the wanted product style. This makes plastic extrusion an ideal remedy for markets that require tailored plastic parts, such as vehicle, building, and product packaging. The capacity to generate diverse items is not just helpful in conference specific market demands yet additionally in making it possible for producers to discover new line of product with marginal capital expense. Fundamentally, plastic extrusion's item adaptability fosters technology while improving operational efficiency.
Enhanced Manufacturing Speed
A significant advantage of plastic extrusion depends on its boosted production speed. This manufacturing procedure enables high-volume manufacturing in a reasonably brief time period. It can generating long, constant plastic accounts, which significantly minimizes the production time. This high-speed production is specifically useful in industries where huge amounts of plastic components are needed within tight due dates. Few other production processes can match the rate of plastic extrusion. In addition, the ability to maintain constant high-speed production without sacrificing item quality establishes plastic extrusion apart from various other approaches. The improved production speed, for that reason, not just makes it possible for suppliers to meet high-demand orders but additionally adds to raised effectiveness and cost-effectiveness. This helpful attribute of plastic extrusion has actually made it a recommended choice in various industries.
Real-world Applications and Influences of Plastic Extrusion
In the realm of production, the method of plastic extrusion holds extensive value. This procedure is commonly used in the manufacturing of a range of items, such as plastic tubes, window structures, and weather condition stripping. Therefore, it significantly affects markets like building and construction, product packaging, and automobile sectors. In addition, its effect reaches day-to-day things, from plastic bags to toothbrushes and non reusable flatware. The economic benefit of plastic extrusion, largely its high-volume and affordable outcome, has reinvented production. The ecological impact of plastic waste stays a concern. Consequently, the industry is persistently pursuing innovations in biodegradable and recyclable materials, indicating a future where the advantages of plastic extrusion can be retained without compromising environmental sustainability.
Final thought
In final thought, plastic extrusion is a very efficient and effective method of transforming resources into varied products. It provides countless benefits over various other plastic developing approaches, consisting of cost-effectiveness, high outcome, minimal waste, and style versatility. Its impact special info is profoundly really felt in different industries such as building and construction, vehicle, and durable goods, making it a pivotal procedure in today's manufacturing landscape.
Delving deeper into the technological process of plastic extrusion, it starts with the selection of the ideal plastic material. Once cooled down, the plastic is cut into the required sizes or wound onto reels if the product is a plastic film or sheet - plastic extrusion. Comparing Plastic Extrusion to Various Other Plastic Forming Methods
Comprehending the types of plastic suitable for extrusion leads the way for a more comprehensive plastic extrusion conversation on just how plastic extrusion stacks up versus other plastic developing approaches. Few various other manufacturing processes can match the speed of plastic extrusion.
Report this page